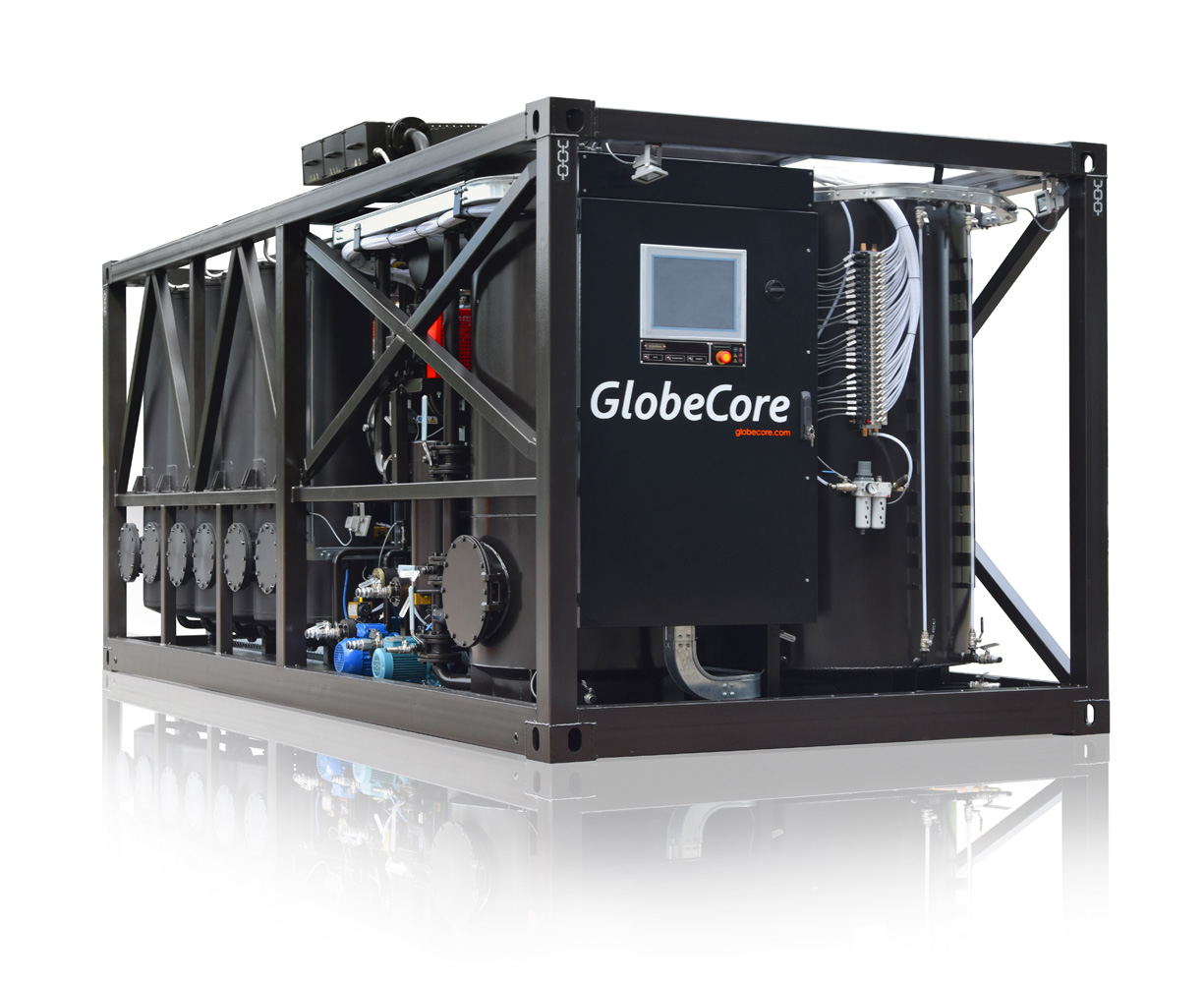
15 de Noviembre de 2015 los empleados de GlobeCore completaron su trabajo bajo el contrato de producción, suministro, comisionado y puesta en marcha de la nueva unidad de regeneración de aceite de CMM-12R en la ciudad El Paso, Texas, EE.UU.
Éste equipo está diseñado para la regeneración completa del aceite dieléctrico aislante en los transformadores modernos eléctricos de potencia. La característica principal de la unidad de regeneración CMM-12R está en que la unidad está apta procesar el aceite sin tener que vaciar y/o recargar los patrones de sorbente con Tierra Fuller, mientras el transformador está energizado. La unidad puede reactivar Tierra Fuller automaticamente, eliminando de esa forma la necesidad de desenergizar el transformador para procesar el aceite.
Conectar el equipo al transformador no tomaría mucho tiempo y puede ser efectuado por solo una persona. Una vez montado, el equipo ya está completamente automatizado. La unidad puede estar operada de veinticuatro horas con un solo operador ubicado en el habitáculo de control con su calentamiento y aire acondicionado y equipado con la computadora. Adicionalmente, la unidad CMM-12R puede estar controlada por medio de las comunicaciónes móviles remotas a través del módulo específico de GSM.
Al trabajar con los aceites aislantes con los inhibidores, la unidad opcional adicional puede injectar los inhibidores aditivos al aceite y así mejorará la resistencia del aceite a la contaminación y a la oxidación.
Los equipos de regeneración GlobeCore se caracterizan por su alta calidad y por la simpicidad en la operación. Se realiza muy poca pérdida de aceite durante el proceso de regeneración y los cambios del peso se deben solamente a la retirada del agua y de la humedad.
Especificaciones técnicas de CMM-R12
Descripción del parámetro |
Valor |
||
1. Nivel de flujo recomendado m3/gals, |
4/1059 |
||
2. Peso total del adsorbente en la unidad, kg/lbs, no menos |
1600/3536 |
||
3 Cantidad de aceite regenerado con la acidez 0.15 mg KOH/g por un ciclo, litros/galones, no menos |
6400/1690 |
||
4 Parámetros de aceite procesado: | |||
Fineza de filtración, μm, no mas |
3 |
||
Número acídico, mg KOH/g de acuerdo a IEC 296; ASTM D-664 |
0.01 |
||
Azufre corrosivo de acuerdo a ISO 5662; ASTM D-1275 |
ausente |
||
Tensión superficial, N/m, a los 25ºС de acuerdo a ISO 6295; ASTM D-2285 |
45 |
||
Tangente de perdidas dieléctricas a los 90ºС de acuerdo a IEC 247; ASTM D-924 |
0.001 |
||
5 Presión de salida, bar, no menos |
1.5 |
||
6 Potencia maxima en la entrada, kW, no mas |
45 |
||
7 Parámetros eléctricos: | |||
Voltage, V |
380-485 |
||
Alternando con la frecuencia, Hz |
50/60 |
||
8 Dimensiones exteriores, mm/pulgadas | |||
Ancho |
2090/82.3 |
||
Alto |
2102/82.76 |
||
Largo |
5150/203.11 |
Por favor, observe nuestro pequeño fotoreportaje de los resultados del exitoso arranque de la unidad GlobeCore CMM-12R en El Paso.