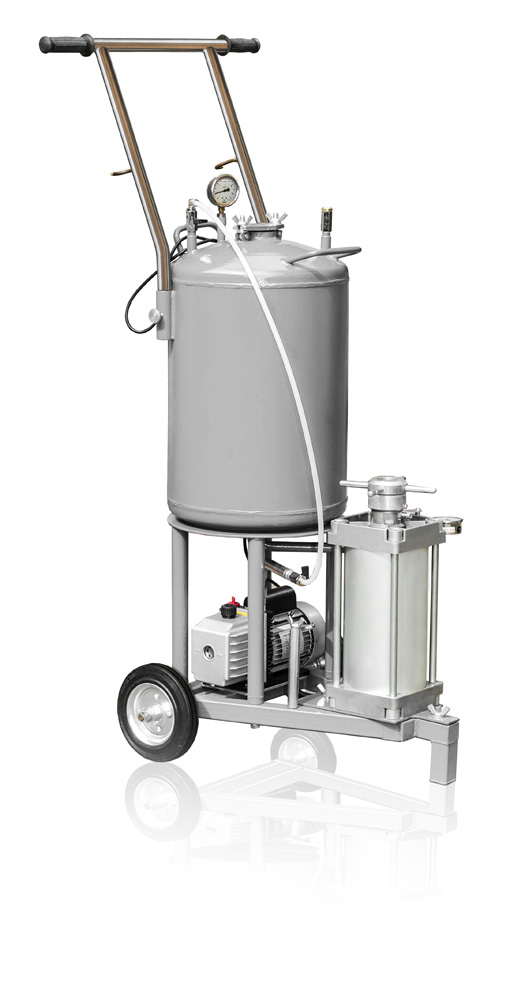
The service life of modern manufacturing equipment is 60% determined by oil quality. A wide range of negative factors that influence machine oil includes:
- temperature;
- environment;
- chemical interaction with other materials; and
- electrical fields (for dielectric oils).
If oil has lost its protective properties, it will affect the engine (namely the wear rate will increase). You should filter oil to prevent such negative consequences.
The GlоbeCоre mobile oil stations are used for oil filtration. They have the following performance characteristics: (1) energy efficiency; (2) cost-effectiveness and (3) a high-quality filtration process.
But, how will we know that oil needs filtration? An incomplete oil filtration process may result in great finance expenditures. It is therefore, a systematic monitoring of oil that is needed to detect changes of the oil’s performance characteristics.
There are two different ways of oil monitoring that depend on the kind of oil the operators want to examine. It is therefore, desirable to follow recogized international standards concerning each specific oil type when the quality of initial oil product is to be tested and analyzed.
Regonized international standards specify the necessary performance characteristics of oil such as: (1) viscosity; (2) ignition temperature; (2) flash temperature, and (3) total base number.
The second way of testing oil is applied when you want to check the quality of oil that has been already used for some period of time. In this case, you may also rely on parameters outlined in the international standards. There are also other possible ways of checking the used oil. The “tribodiagnostic” process allows the operator to check the condition of machinery without overhaul or disassembly through the use of oil analysis. This method however, has not gained widespread acceptance and is mostly used when examining and servicing gas-turbine engines. The tribodiagnostic consists of the assessment of the composition and the concentration of wear products in oil using special devices (e.g. spectrometer).
The ferrography is used to determine the wear type and friction rate of the machinery. This process consists of analysing the particle size distribution, their surface condition and the materials they are composed of.
The advantage of this method is that it can be used when working with magnetic as well as non-magnetic materials (graphite, bronze, aluminum, brass, etc.). Infrared (IR) spectroscopy allows the operators to receive information about such important oil specifications as water content, base number, acid number, soot content, additives, and oxidation products.
The proper sampling is no less important than the analysis itself since the wrong sample may lead to an incorrect diagnosis of the equipment.